Experience Excellence: Premier Pipeline Welding Inspection Services You Can Depend On
Experience Excellence: Premier Pipeline Welding Inspection Services You Can Depend On
Blog Article
Crucial Pipe Welding Evaluation Tips for Quality Control
In the world of pipeline building, the stability of welds holds vital significance to guarantee the safety and security and effectiveness of the whole system. From gas to refined oil products, pipelines form the lifeline of various sectors. How can one ensure the top quality of these welds that link the pipe sections? The response hinges on meticulous inspection strategies and adherence to stringent quality control criteria. By understanding the crucial pipe welding inspection ideas, experts can avert possible threats, decrease costly repair work, and maintain the reliability of these essential infrastructures.

Importance of Welding Examination
Welding examination plays an essential role in making certain the structural integrity and safety and security of pipeline systems. By thoroughly analyzing welds, inspectors can recognize any flaws or blemishes that could endanger the integrity of the pipeline. These assessments are necessary for preventing leaks, tears, and various other potentially disastrous failings that might lead to environmental damage, financial losses, and even loss of life.
The value of welding inspection can not be overemphasized, as the high quality of welds directly impacts the general efficiency and durability of the pipe. Through non-destructive screening methods such as aesthetic evaluation, ultrasonic screening, radiography, and magnetic bit testing, assessors can detect problems that may not show up to the naked eye. By recognizing and resolving these problems beforehand, welding examination assists to make sure that pipelines meet industry requirements and regulative demands.
Ultimately, welding evaluation is a crucial element of quality control in pipeline upkeep, construction, and repair service (Pipeline Welding Inspection). By supporting rigorous inspection requirements, industry professionals can alleviate risks and maintain the safety and security and dependability of pipe systems
Usual Welding Defects
Amongst the difficulties dealt with in pipeline welding, usual issues can dramatically impact the architectural stability and efficiency of the bonded joints. Fractures in the weld can propagate over time, endangering the structural integrity of the pipe. Identifying and dealing with these usual issues via complete assessment and top quality control procedures are vital for making sure the integrity and safety and security of pipeline welds.
Examination Techniques for Pipes
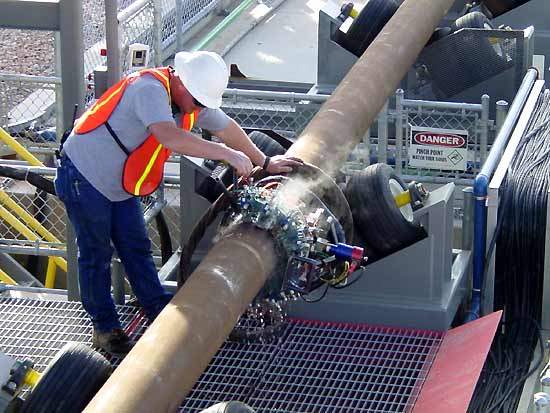

In making certain the architectural integrity and reliability of pipeline welds, the application of strenuous evaluation methods is paramount. Numerous examination methods are employed to identify potential flaws and guarantee the overall top quality of the welds. Non-destructive screening (NDT) strategies such as radiographic testing, ultrasonic testing, magnetic particle testing, and liquid penetrant screening are generally used in pipeline welding evaluation. Radiographic testing involves the usage of X-rays or gamma rays to identify internal problems, while ultrasonic testing makes use of high-frequency sound waves to identify imperfections. Magnetic particle testing is reliable for identifying surface-breaking problems, and liquid penetrant testing is used to discover surface area fractures. Aesthetic inspection is additionally vital in pipeline welding to identify any kind of visible issues or interruptions. Additionally, automated evaluation techniques using sophisticated technologies like robotics and drones are increasingly being employed to boost the effectiveness and accuracy of pipe assessments. By using a combination of these assessment strategies, pipe bonded high quality can be guaranteed, and prospective issues can be alleviated before they escalate right into larger issues.
Making Certain Quality Guarantee Requirements
To maintain rigid quality control requirements in pipe building, precise adherence to my explanation established industry procedures and standards is essential. Quality control in welding processes needs a comprehensive strategy including different stages of pipe construction. Ensuring the high quality of welds includes the use of qualified welders, correct welding treatments, and adherence to industry requirements such as those set by the American Petroleum Institute (API) and the American Culture of Mechanical Designers (ASME) Inspection and screening play a vital function in validating the stability of welds, with strategies like non-destructive screening (NDT) being critical for spotting possible issues. In addition, maintaining detailed documentation throughout the welding procedure is essential for traceability and top quality control objectives. Implementing a robust high quality management system that includes normal audits and evaluations can further enhance the general quality control criteria in pipe welding. By focusing on adherence to these criteria, stakeholders can make certain the integrity and safety and security of pipeline systems for the long-term.
Stopping Pricey Repair Work
Given the vital value of preserving rigorous quality guarantee standards in pipe building, an aggressive technique to preventing costly repairs is crucial. Routine upkeep checks and tracking of environmental factors that could affect the stability of the pipeline are likewise critical in protecting against expensive repair services. By spending in preventative procedures and focusing on top quality assurance at every phase of the pipe welding procedure, firms can decrease the threat of expensive repair services and ensure the long-lasting dependability of their infrastructure.
Verdict
In conclusion, adherence to proper welding assessment techniques is crucial for making sure the high quality and stability of pipes. By recognizing usual welding flaws and applying detailed examination procedures, costly repair work can be stopped, and quality control criteria can be fulfilled - Pipeline Welding Inspection. It is essential for pipeline welders to prioritize inspection procedures to maintain the safety and reliability of the framework they are servicing
The importance of welding examination can not be overemphasized, as the quality of welds directly influences the total efficiency and durability of the pipe. Non-destructive testing (NDT) techniques such as radiographic screening, ultrasonic testing, magnetic bit screening, and liquid penetrant screening are commonly utilized in pipeline welding evaluation. Aesthetic inspection is also essential in pipeline welding to recognize any noticeable defects or click here now suspensions. In addition, computerized inspection strategies utilizing advanced technologies like robotics and drones are increasingly being utilized to enhance the performance and precision of pipe inspections.In final thought, adherence to correct welding inspection techniques is crucial for official site making certain the high quality and honesty of pipelines.
Report this page